Consequences of the choice of clays and manufacturing methods of Ollas
To make irrigation Ollas , it is necessary to choose the clays used carefully and to adapt the manufacturing method accordingly.
It is a complex process, on which Poterie Jamet has worked for many years in research and development to obtain Ollas offering the highest level of quality.
Our know-how is at the heart of each of our ollas with the most demanding quality control.
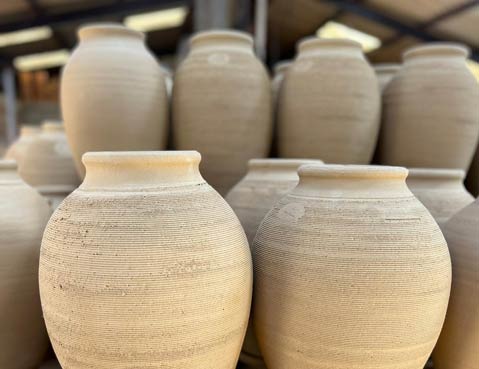
For the most part, these are so-called “washed” pastes which are soaked in baths and then filtered.
This process has the advantage of having a material that is inexpensive, quick to produce and easy to turn.
Due to the filtration of the impurities, these "washed" pastes retain little or no residual soil grains, which makes a compact paste with little air in the natural micro-veins and gives less good porosity.
To compensate for this lack of water flow, it will be necessary to turn jars with thin walls, therefore more fragile to shocks, otherwise they would become too tight, but also more sensitive to microcracks.
Conversely, pastes to be shaped with dry ground earth will give a mixture with a natural grain allowing a dense and regular micro-veining which will give an excellent porosity and structure of the ceramic, whatever the thickness of this one. .
The dry ground technique requires more tools and much more preparation time.
Depending on the desired production quality, the dough to be shaped, after its mixing (mixture of earth and water) and before its extrusion (production of clay blocks before turning), can be left to rest for several days or weeks depending on weather conditions at the time and on the calendar.
This so-called “rotting” phase – (resting in pottery language), allows additional fermentation which ensures perfect homogeneity for turning and drying resistance, resistance after firing and finally regular porosity.
This is an essential step that lasts at least 15 days for the production of quality ceramics.
The design of a molding paste with dry ground earth and long rest times gives a raw material to be molded of very high quality, but it is more expensive and takes longer to manufacture.
In addition, it is less malleable than "washed pastes", which requires longer turning times when making ceramics.
Clays made from dry-ground earth also make it possible to make more resistant Ollas because they are thicker and larger in volume thanks to their structural qualities.
They will also help to avoid the subsequent risk of microcracking during drying, firing and after firing.
Once the ceramics have been shaped, a long drying time must be allowed at room temperature, which is adjusted according to the weather conditions, the size and the weight of the pieces to be dried.
This allows the ceramics to dry gently, without rushing them, keeping the homogeneity of their internal structure intact.
This simple, but essential, operation requires the necessary time because it contributes to the mechanical resistance of the ceramics and prevents them from cracks and micro-cracks.
The drying, carried out sheltered from the wind and the direct sun, makes it possible to evacuate the major part of the water.
The drying speed is mainly due, not to the temperature, but to two independent factors (or almost):
- The humidity level of the air:
Indeed in the tropics with 90% humidity level, your parts will dry with difficulty or not at all even with a low 45°C in the shade…. - Gas exchange
The renewal of the air will dry the parts quickly under dry air.
This phenomenon can lead to deformation of the parts, or even cracking of the latter in the event that the part does not dry uniformly and/or too quickly.
Quick drying is in any case to be avoided, especially for the production of irrigation jars.
Otherwise, by reducing the drying times, the risks of visible cracking (bursting) and not directly visible (microcrack) are increased all the more.
This last case will impact the operation of the jar which will leak too much and will ultimately have a negative effect on the quality (*) of the soil. (*) See next section Microcrack.
Nevertheless, for low quality productions or rushed productions, there is drench … -> If you are late for an order and/or there is too much ambient humidity, there is a solution. Preheating the objects in a kiln evacuates the surface water before the actual firing.
This last technique consists of putting the parts in an oven at a temperature below 100°C!
In general, 80°C is displayed for… the time it takes for the parts to finally dry. It can last from 3 to 12 hours or even more… (here, we are not in ecology…).
Heating the oven will create an expansion of the air contained in the oven and therefore a slight overpressure inside it.
This phenomenon will evacuate part of the heated air and create a suction of cold air through the openings of the oven (vents, cracks, doors, etc.).
Even in an electric oven, a gaseous exchange will take place between the outside and the inside of the oven.
This drying will therefore lead to a start of shrinkage of 2 to 8%. This phenomenon is due to the evaporation of water which is transformed into gas. This causes the molecules to come closer together.
Microcracks are the result of a structural defect caused most of the time by the following steps:
- Elaboration of unsuitable shaping dough.
- Drying and cooking times too short.
- Temperatures too high during drying.
- Cooking management.
Cracks or bursts more or less important and visible after firing make the ceramic unusable. It cannot be sold as is. At best, the ceramic will be finely ground to make a "chamotte" for potters who need this material in other collections.
More difficult to detect, ceramics which have not burst when leaving the oven, but which have microcracks. In the case of production for irrigation ceramics, this will have a negative impact on the areas to be irrigated.
Indeed the micro cracked jar will leak much more than normal. Generally there is an autonomy and irrigation area divided by 2, or even more.
It will release too much water in the same place and permanently.
This situation is worse than soil that is too dry, because repeated excess water will pack down / compact the soil, reducing or stopping bacterial life.
However, this is essential for the microbial and biological life of the soil to provide fresh and airy soils, conducive to the development of plants.
To avoid this defect, which is difficult to detect, each batch must be checked by checking the porosity of the jars.
Final stage of the irrigation jar manufacturing process, the duration, the different temperature levels and the maximum cooking temperature reached, vary greatly from one factory to another and depend on the previous stages.
During cooking, voids will be created by the evaporation of water and carbonaceous elements, which represent approximately 20% of the initial volume (this does not create 20% shrinkage).
The modification of the clay by firing will make it possible to develop new properties:
- Mechanical and thermal resistance
- Low or high porosity
- Thermal conductivity
- Sometimes translucent
Depending on the maximum temperature reached, the transformations of the paste and the products obtained vary (terracotta, earthenware, stoneware, porcelain).
Modifications of the structure during the evolution of the temperature.
- up to 200°C, surface water is evacuated (pre-heating)
- from 200 to 450°C, organic matter oxidizes and is destroyed at 700°C
- from 450°C to 650°C, the structure of clay materials begins to break down
- from 650°C to 800°C the decomposition of calcium carbonate takes place
- from 800 to 1100°C, there is a gradual "sanding" of the clay under the effect of the "melters"
Departure from the different waters (from):
- Imbibition water: > 0°C, during shaping
- Colloidal water: > 0°C, during manufacturing drying and firming (leather condition)
- Interposition water: 23 to 100°C, during drying and at the start of cooking (change to vapor state!!).
- Hygrometric water: up to 350°C, bleeding at the start of cooking.
- Water of constitution of kaolinite: 450°C.
- At 550°C all the water has disappeared, the clay can no longer be rehydrated!
Evolution of clays during firing:
- from 0 to 100°C, during drying: departure of interposition water at 100°C transition to vapor state. Risk of bursting parts.
- from 200 to 450°C, organic matter oxidizes producing degassing. Same risk as above.
- Point Quartz: when the temperature rises, the quartz crystals arrange themselves in a different order.
Around 573°C a change in volume (about 2%) occurs.
Alpha quartz turns into beta quartz. This change is reversible on cooling.
These variations in volume can cause the part to crack if the rise or fall in temperature is too rapid in relation to the capacities of the dough to be shaped.
It should be understood that these are real temperatures at the heart of the parts and should be taken into account all the more if the parts are thick.
Some parts may have parts of different thicknesses (thin parts compared to the rest of them, thin walls on a thick bottom, bonding thinner parts).
In the latter cases, if the rise is too rapid, there is a risk of cracking at the thin/thick junction because the expansion does not take place simultaneously.
Cooking an irrigation jar with “washed” paste
The “washed” clay jars are fired at low temperature, below 1,000°C, to achieve an effective porosity (about 18 to 20%, if fired at 850/1,000°C).
Beyond 1,000°C, this would greatly reduce the porosity of the jar, or even make it completely waterproof.
This paste does not have enough micro-veining, because it is too compact due to a lack of natural grain and combined with the shrinkage of the jar after drying and cooking, it does not ensure normal porosity at high temperatures. (>1.000°C°).
On the other hand, it is recommended not to cook the jars at too low a temperature, otherwise they risk breaking by chemical reaction in contact with a soil that is too calcareous or saline.
Production with this type of paste, due to its structure and the low thickness of the parts produced, is subject to irregular porosity (too tight or micro-leaks) due to one or all of the previous phases.
However, its production is achievable in one week and therefore inexpensive to produce, but is limited to containers of a maximum of 10 liters.
If the “washed” paste jar is not sufficiently permeable, it is possible to lightly sand the external surface, and thus increase the hydraulic conductivity up to 30%.
The pottery should never be glazed.
Firing an irrigation jar with "dry ground" paste
Conversely, "dry ground" pastes have significant and regular micro-veining thanks to the high density of their natural grain and can be fired above 1,050/1,100°C while retaining excellent porosity, without excess if we respect the manufacturing process but more complex and long.
This makes it possible to produce large capacity jars (>35 Liters) which will have a high structural resistance and will be insensitive to frost.