Consecuencias de la elección de arcillas y métodos de fabricación de Ollas
Para hacer Ollas de riego , es necesario elegir cuidadosamente las arcillas utilizadas y adaptar el método de fabricación en consecuencia.
Es un proceso complejo, en el que Poterie Jamet ha trabajado durante muchos años en investigación y desarrollo para obtener ollas que ofrezcan el más alto nivel de calidad.
Nuestro saber hacer está en el corazón de cada una de nuestras ollas con el control de calidad más exigente.
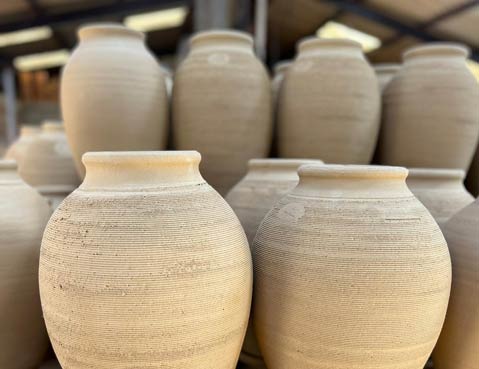
En su mayor parte, se trata de las llamadas pastas "lavadas" que se sumergen en baños y luego se filtran.
Este proceso tiene la ventaja de tener un material económico, rápido de producir y fácil de tornear.
Debido a la filtración de las impurezas, estas pastas "lavadas" retienen poco o ningún grano residual del suelo, lo que hace una pasta compacta con poco aire en las microvenas naturales y da una porosidad menos buena.
Para compensar esta falta de flujo de agua, será necesario dar la vuelta a los recipientes con paredes delgadas, por lo tanto, más frágiles a los golpes, de lo contrario quedarían demasiado apretados, pero también más sensibles a las microfisuras.
Por el contrario, las pastas para conformar con tierra seca molida darán una mezcla con un grano natural permitiendo un micro-veteado denso y regular que dará una excelente porosidad y estructura a la cerámica, cualquiera que sea el espesor de ésta.
La técnica de tierra seca requiere más herramientas y mucho más tiempo de preparación.
Dependiendo de la calidad de producción deseada, la masa a moldear, después de su amasado (mezcla de tierra y agua) y antes de su extrusión (producción de bloques de arcilla antes del torneado), se puede dejar reposar durante varios días o semanas según las condiciones climáticas. en el momento y en el calendario.
Esta fase denominada “podredumbre” (reposo en el lenguaje cerámico), permite una fermentación adicional que asegura una perfecta homogeneidad para la resistencia al torneado y al secado, resistencia después de la cocción y finalmente una porosidad regular.
Este es un paso esencial que dura al menos 15 días para la producción de cerámica de calidad.
El diseño de una pasta de moldeo con tierra molida seca y largos tiempos de reposo da una materia prima a moldear de muy alta calidad, pero es más costosa y lleva más tiempo su fabricación.
Además, es menos maleable que las “pastas lavadas”, que requieren mayores tiempos de torneado al fabricar cerámica.
Las arcillas de tierra molida en seco también permiten hacer Ollas más resistentes porque son más gruesas y voluminosas gracias a sus cualidades estructurales.
También ayudarán a evitar el riesgo posterior de microgrietas durante el secado, la cocción y después de la cocción.
Una vez moldeada la cerámica, se debe dejar un largo tiempo de secado a temperatura ambiente, que se ajusta según las condiciones climáticas, el tamaño y el peso de las piezas a secar.
Esto permite que las cerámicas se sequen suavemente, sin apurarlas, manteniendo intacta la homogeneidad de su estructura interna.
Esta operación sencilla, pero imprescindible, requiere el tiempo necesario porque contribuye a la resistencia mecánica de las cerámicas y evita que se agrieten y microfisuras.
El secado, realizado al abrigo del viento y del sol directo, permite evacuar la mayor parte del agua.
La velocidad de secado se debe principalmente, no a la temperatura, sino a dos factores independientes (o casi):
- El nivel de humedad del aire:
De hecho, en los trópicos con un nivel de humedad del 90%, sus partes se secarán con dificultad o no se secarán en absoluto, incluso con un bajo 45°C a la sombra…. - Intercambio de gases
La renovación del aire secará las piezas rápidamente bajo aire seco.
Este fenómeno puede conducir a la deformación de las piezas, o incluso al agrietamiento de las mismas en el caso de que la pieza no se seque uniformemente y/o demasiado rápido.
En cualquier caso, debe evitarse el secado rápido, especialmente para la producción de jarras de riego.
En caso contrario, al reducir los tiempos de secado, aumentan aún más los riesgos de fisuración visible (estallido) y no directamente visible (microfisura).
Este último caso repercutirá en el funcionamiento de la jarra, que filtrará demasiado y, en última instancia, repercutirá negativamente en la calidad (*) del suelo. (*) Ver apartado siguiente Microfisura.
Sin embargo, para producciones de baja calidad o producciones apresuradas, hay empape… -> Si llega tarde a un pedido y/o hay demasiada humedad ambiental, hay una solución. El precalentamiento de los objetos en un horno evacua el agua superficial antes de la cocción real.
¡Esta última técnica consiste en poner las piezas en un horno a una temperatura inferior a 100°C!
En general, 80°C se muestra para... el tiempo que tardan las piezas en secarse finalmente. Puede durar de 3 a 12 horas o incluso más… (aquí no estamos en ecología…).
El calentamiento del horno provocará una dilatación del aire contenido en el horno y por tanto una ligera sobrepresión en su interior.
Este fenómeno evacuará parte del aire caliente y creará una succión de aire frío a través de las aberturas del horno (ventilaciones, grietas, puertas, etc.).
Incluso en un horno eléctrico se producirá un intercambio gaseoso entre el exterior y el interior del horno.
Este secado conducirá por lo tanto a un inicio de contracción del 2 al 8%. Este fenómeno se debe a la evaporación del agua que se transforma en gas. Esto hace que las moléculas se acerquen.
Las microfisuras son el resultado de un defecto estructural causado la mayoría de las veces por los siguientes pasos:
- Elaboración de masa moldeadora no apta.
- Tiempos de secado y cocción demasiado cortos.
- Temperaturas demasiado altas durante el secado.
- Manejo de cocina.
Grietas o estallidos más o menos importantes y visibles después de la cocción inutilizan la cerámica. No se puede vender como está. En el mejor de los casos, la cerámica se triturará finamente para hacer una "chamota" para los alfareros que necesiten este material en otras colecciones.
Más difíciles de detectar, las cerámicas que no han reventado al salir del horno, pero que presentan microfisuras. En el caso de la producción de cerámica para riego, esto tendrá un impacto negativo en las áreas a regar.
De hecho, el frasco micro agrietado goteará mucho más de lo normal. Generalmente hay una autonomía y zona de riego dividida por 2, o incluso más.
Liberará demasiada agua en el mismo lugar y de forma permanente.
Esta situación es peor que la del suelo demasiado seco, porque el exceso de agua repetido empacará/compactará el suelo, reduciendo o deteniendo la vida bacteriana.
Sin embargo, esto es esencial para la vida microbiana y biológica del suelo para proporcionar suelos frescos y aireados, propicios para el desarrollo de las plantas.
Para evitar este defecto, que es difícil de detectar, cada lote debe ser controlado comprobando la porosidad de los tarros.
Etapa final del proceso de fabricación de las jarras de riego, la duración, los diferentes niveles de temperatura y la temperatura máxima de cocción alcanzada, varían mucho de una fábrica a otra y dependen de las etapas anteriores.
Durante la cocción, se crearán vacíos por la evaporación del agua y los elementos carbonosos, que representan aproximadamente el 20 % del volumen inicial (esto no crea una contracción del 20 %).
La modificación de la arcilla por cocción permitirá desarrollar nuevas propiedades:
- Resistencia mecánica y térmica
- Baja o alta porosidad
- Conductividad térmica
- A veces translúcido
Según la temperatura máxima alcanzada, varían las transformaciones de la pasta y los productos obtenidos (terracota, loza, gres, porcelana).
Modificaciones de la estructura durante la evolución de la temperatura.
- hasta 200°C, se evacua el agua superficial (precalentamiento)
- de 200 a 450°C, la materia orgánica se oxida y se destruye a 700°C
- de 450°C a 650°C, la estructura de los materiales arcillosos comienza a descomponerse
- de 650°C a 800°C se produce la descomposición del carbonato de calcio
- de 800 a 1100°C, hay un "lijado" gradual de la arcilla bajo el efecto de los "fundidores"
Salida desde las diferentes aguas (desde):
- Agua de imbibición: > 0°C, durante la conformación
- Agua coloidal: > 0°C, durante la fabricación, secado y endurecimiento (estado del cuero)
- Agua de interposición: 23 a 100°C, durante el secado y al inicio de la cocción (cambio a estado vapor!!).
- Agua higrométrica: hasta 350°C, sangrado al inicio de la cocción.
- Agua de constitución de caolinita: 450°C.
- A 550°C toda el agua ha desaparecido, ¡la arcilla ya no se puede rehidratar!
Evolución de las arcillas durante la cocción:
- de 0 a 100°C, durante el secado: salida del agua de interposición a 100°C transición al estado de vapor. Riesgo de explosión de piezas.
- de 200 a 450°C, la materia orgánica se oxida produciendo desgasificación. Mismo riesgo que el anterior.
- Punto Cuarzo: cuando sube la temperatura, los cristales de cuarzo se disponen en un orden diferente.
Alrededor de 573°C se produce un cambio de volumen (alrededor del 2%).
El cuarzo alfa se convierte en cuarzo beta. Este cambio es reversible al enfriarse.
Estas variaciones de volumen pueden hacer que la pieza se agriete si la subida o bajada de temperatura es demasiado rápida en relación con las capacidades de la masa a moldear.
Debe entenderse que estas son temperaturas reales en el corazón de las piezas y deben tenerse en cuenta tanto más si las piezas son gruesas.
Algunas partes pueden tener partes de diferentes espesores (partes delgadas con respecto al resto, paredes delgadas sobre un fondo grueso, unión de partes más delgadas).
En estos últimos casos, si el ascenso es demasiado rápido, existe el riesgo de agrietamiento en la unión delgada/gruesa porque la expansión no se produce simultáneamente.
Cocción de una jarra de riego con pasta “lavada”
Las vasijas de barro “lavadas” se cuecen a baja temperatura, por debajo de los 1.000 °C, para lograr una porosidad efectiva (alrededor del 18 al 20 %, si se cuecen a 850/1.000 °C).
Más allá de los 1000°C, esto reduciría en gran medida la porosidad del frasco, o incluso lo haría completamente impermeable.
Esta pasta no tiene suficiente micro-veteado, porque es demasiado compacta por falta de grano natural y combinado con el encogimiento del tarro después del secado y la cocción, no asegura una porosidad normal a altas temperaturas. (>1.000°C°).
Por otro lado, se recomienda no cocinar los tarros a una temperatura demasiado baja, de lo contrario corren el riesgo de romperse por reacción química en contacto con un suelo demasiado calcáreo o salino.
La producción con este tipo de pasta, debido a su estructura y al bajo espesor de las piezas producidas, está sujeta a porosidad irregular (demasiado apretada o microfugas) por alguna o todas las fases anteriores.
Sin embargo, su producción es alcanzable en una semana y por lo tanto económica de producir, pero está limitada a envases de un máximo de 10 litros.
Si el tarro de pasta “lavado” no es lo suficientemente permeable, es posible lijar ligeramente la superficie externa y así aumentar la conductividad hidráulica hasta un 30%.
La cerámica nunca debe ser esmaltada.
Cocción de una jarra de riego con pasta "tierra seca"
Por el contrario, las pastas "molidas en seco" presentan un importante y regular microveteado gracias a la alta densidad de su grano natural y pueden cocerse por encima de 1.050/1.100°C conservando una excelente porosidad, sin excesos si respetamos el proceso de fabricación pero más complejo y largo.
Esto permite producir tinajas de gran capacidad (>35 Litros) que tendrán una alta resistencia estructural y serán insensibles a las heladas.