Conséquences du choix des argiles et méthodes de fabrication des Ollas
Pour réaliser des Ollas d’irrigation de qualité, il est nécessaire de bien choisir les argiles utilisés et d’adapter la méthode de fabrication en fonction.
Il s’agit d’un processus complexe, sur lequel Poterie Jamet a travaillé de nombreuses années en recherche et développement pour obtenir des Ollas offrant la plus haut niveau de qualité.
Notre savoir-faire est au coeur de chacune des nos ollas avec un contrôle qualité des plus exigeants.
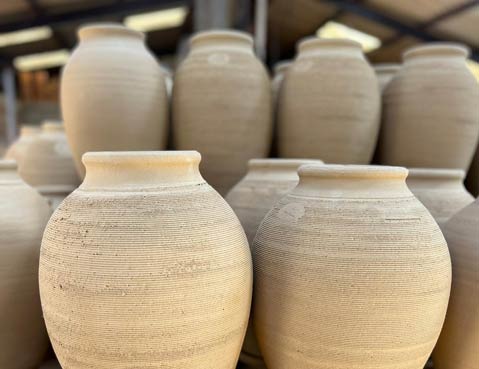
Pour la plupart, ce sont des pâtes dites « lavées » qui sont trempées dans des bains, puis filtrées.
Ce procédé a l’avantage d’avoir une matière peu chère, rapide à produire et facile à tourner.
Du fait de la filtration des impuretés, ces pâtes « lavées » ne conservent pas ou peu les grains résiduels des terres, ce qui fait une pâte compacte avec peu d’air dans les micro-veines naturelles et donne une moins bonne porosité.
Pour compenser ce manque d’écoulement d’eau on sera obligé de tourner des jarres avec des parois peu épaisses, donc plus fragiles aux chocs, sinon elles deviendraient trop étanches, mais aussi plus sensibles aux microfissures.
A l’inverse, les pâtes à façonner avec des terres broyées à sec donneront un mélange au grain naturel permettant un micro-veinage dense et régulier qui donnera une excellente porosité et structure de la céramique, quelle que soit l’épaisseur de celle-ci.
La technique des terres broyées à sec nécessite plus d’outillage et beaucoup plus de temps de préparation.
Selon la qualité de production recherchée, la pâte à façonner, après son malaxage (mélange des terres et de l’eau) et avant son extrusion (fabrication des pains d’argile avant tournage), peut être laissée au repos plusieurs jours ou semaines selon les conditions climatiques du moment et du calendrier.
Cette phase dite de « pourrissement » – (de repos en langage potier), permet une fermentation additionnelle qui lui assure une homogénéité parfaite pour la tenue au tournage et au séchage, la résistance après cuisson et enfin une porosité régulière.
C’est une étape primordiale qui dure minimum 15 jours pour la réalisation de céramiques de qualité.
La conception d’une pâte à façonner avec des terres broyées à sec et des temps de repos long donnent une matière première à façonner de très grande qualité, mais elle est plus chère et plus longue à fabriquer.
De plus, elle est moins malléable que les « pâtes lavées » ce qui nécessite des temps de tournage plus long, lors de la confection des céramiques.
Les pâtes à façonner en terres broyées à sec permettent aussi de faire des Ollas plus résistantes car plus épaisses et de plus gros volume grâce à leurs qualités structurelles.
Elles contribueront aussi à éviter le risque ultérieur de microfissure au séchage, à la cuisson et après cuisson.
Une fois les céramiques façonnées, il faut laisser un temps de séchage long à température ambiante qui est ajusté selon les conditions météo, la taille et le poids des pièces à sécher.
Cela permet aux céramiques de sécher doucement, sans les brusquer en gardant intact l’homogénéité de leur structure interne.
Cette opération simple, mais essentielle, nécessite le temps qu’il faut car elle contribue à la résistance mécanique des céramiques et leur évite des fissures et microfissures.
Le séchage, réalisé à l’abri du vent et du soleil direct, permet d’évacuer la majeure partie de l’eau.
La vitesse de séchage est due principalement, non pas à la température qu’il fait, mais à deux facteurs indépendants (ou presque) :
- Le taux d’humidité de l’air:
En effet sous les tropiques avec 90% de taux d’humidité, vos pièces sècheront difficilement voir pas du tout même avec un petit 45°C à l’ombre…. - L’échange gazeux
Le renouvèlement de l’air assèchera les pièces rapidement sous un air sec.
Ce phénomène peut engendrer des déformations des pièces, voire des fissurations de celle-ci au cas où la pièce ne sècherait pas uniformément et/ou trop vite.
Un séchage rapide est de toute façon à proscrire en particulier pour la réalisation de jarre d’irrigation.
Sinon en réduisant les temps de séchage, on augmente d’autant plus les risques de fissuration visible (éclatement) et non visible directement (microfissure).
Ce dernier cas impactera le fonctionnement de la jarre qui fuira de trop et produira à terme un effet négatif sur la qualité (*) des sols. (*) Voir rubrique suivante Microfissure.
Néanmoins, pour les productions peu qualitatives ou des réalisations pressées, il existe le bassinage … -> Si on est en retard pour une commande et/ou qu’il y a trop d’humidité ambiante, une solution existe. Un préchauffage des objets dans un four évacue l’eau superficielle avant la cuisson proprement dite.
Cette dernière technique consiste à mettre les pièces dans un four à une température inférieure à 100°C ! En général, on affiche 80°C pendant… le temps qu’il faut pour que les pièces soient enfin sèches.
Cela peut durer de 3 à 12heures voir plus… (là, on n’est pas dans l’écologie…).
Le four en chauffant va créer une dilatation de l’air contenu dans le four et donc une légère surpression à l’intérieur de celui-ci.
Ce phénomène va évacuer une partie de l’air chauffé et créer une aspiration d’air froid pas les ouvertures du four (évents, fissures, portes, …).
Même en four électrique un échange gazeux se fera entre l’extérieur et l’intérieur du four.
Ce séchage va donc entrainer un début de rétractation de 2 à 8%. Ce phénomène est dû à l’évaporation de l’eau qui se transforme en gaz. Ceci entraine un rapprochement des molécules entre elles.
Les microfissures sont la résultante d’un défaut structurel provoqué la plupart du temps par les étapes suivantes :
- Elaboration de pâte à façonner non adaptée.
- Temps de séchage et de cuisson trop courts.
- Températures trop hautes au séchage.
- Gestion de la cuisson.
Les fissures ou éclatements plus ou moins importants et visibles après cuisson rendent la céramique inutilisable. Elle ne peut être vendue en l’état. Au mieux, la céramique sera finement broyée pour en faire une « chamotte » pour les potiers qui ont besoin de cette matière dans d’autres collections.
Plus difficile à détecter, les céramiques qui n’ont pas éclaté en sortie de four, mais qui ont des microfissures. Dans le cas d’une production pour des céramiques d’irrigation cela aura un impact néfaste sur les zones à irriguer.
En effet la jarre micro fissurée va fuir beaucoup plus que la normale. Généralement on constate une autonomie et surface d’irrigation divisée par 2, voire plus.
Elle va libérer trop d’eau au même endroit et en permanence.
Cette situation est pire qu’un sol trop sec, car l’excédent d’eau à répétition va tasser / compacter le sol, diminuant ou stoppant la vie bactérienne.
Or celle-ci est indispensable à la vie microbienne et biologique des sols pour donner des sols frais et aérés, propices à l’épanouissement des végétaux.
Pour éviter ce défaut difficilement détectable, il faut contrôler chaque fournée en vérifiant la porosité des jarres.
Etape finale du processus de fabrication des jarres d’irrigation, la durée, les différents paliers de températures et la température maximale de cuisson atteinte, sont très variables d’une fabrique à l’autre et dépendent des étapes précédentes.
Lors de la cuisson des vides vont se créer par l’évaporation de l’eau et des éléments carbonés, qui représentent 20% environ du volume de départ (Cela ne crée pas 20% de rétractation).
La modification de l’argile par la cuisson va permettre de développer des propriétés nouvelles :
- Résistance mécanique et thermique
- Porosité faible ou élevée
- Conductivité thermique
- Translucidité parfois
Selon la température maximale atteinte, les transformations de la pâte et les produits obtenus varient (terre cuite, faïence, grès, porcelaine).
Modifications de la structure lors de l’évolution de la température.
- jusqu’à 200°C, l’eau superficielle s’évacue (pré-chauffage)
- de 200 à 450 °C, les matières organiques s’oxydent et sont détruites à 700°C
- de 450°C à 650°C, la structure de matériaux argileux commence à se détruire
- de 650°C à 800°C s’effectue la décomposition du carbonate de calcium
- de 800 à 1100°C, il y a « grésage » progressif de l’argile sous l’effet des « fondants »
Départ des différentes eaux (à partir de) :
- Eau d’imbibition : > 0°C, lors de façonnage
- Eau colloïdale : > 0°C, lors du ressuyage de fabrication et du raffermissement (état cuir)
- Eau d’interposition : 23 à 100°C, lors du séchage et du début de cuisson (passage à l’état de vapeur !!).
- Eau hygrométrique : jusqu’à 350°C, ressuage de début de cuisson.
- Eau de constitution de la kaolinite : 450°C.
- A 550 °C toutes les eaux ont disparues, l’argile ne peut plus être réhydratée !
Évolution des argiles au cours de la cuisson :
- de 0 à 100 °C, en cours de séchage : départ de l’eau d’interposition à 100°C passage à l’état de vapeur. Risque d’éclatement des pièces.
- de 200 à 450 °C, les matières organiques s’oxydent produisant un dégazage. Même risque que ci-dessus.
- Point Quartz : lors de la montée en température, les cristaux de quartz se disposent d’eux-mêmes dans un ordre différent.
Aux alentours de 573°C un changement de volume (de l’ordre de 2%) se produit.
Le quartz Alpha se transforme en quartz Béta. Ce changement est réversible au refroidissement.
Ces variations de volume peuvent faire fissurer la pièce si la monté ou la descente en température est trop rapide par rapport aux capacités de la pâte à façonner.
Il faut comprendre que ce sont des températures réelles au cœur des pièces et à en tenir d’autant plus compte si les pièces sont épaisses.
Certaines pièces peuvent avoir des parties de différentes épaisseurs (parties fines par rapport au reste de celles-ci, parois fines sur un fond épais, collage de parties plus fines).
Dans ces derniers cas, si la montée est trop rapide, il y a un risque de fissuration à la jonction fin/épais car la dilatation ne s’effectuant pas simultanément.
Cuisson de jarre d’irrigation à pâte « lavée »
Les jarres à pâte « lavée » sont cuites à faible température, en dessous de 1.000 °C., pour atteindre une porosité effective (d’environ 18 à 20 %, si cuite à 850/1.000°C).
Au-delà des 1.000°C, cela diminuerait fortement la porosité de la jarre, voire de la rendre complétement étanche.
Cette pâte n’a pas assez de micro-veinage, car trop compacte par manque de grain naturel et combiné au retrait de la jarre après séchage et cuisson, elle ne permet pas d’assurer une porosité normale à des températures élevées. (>1.000°C°).
Il est recommandé en revanche de ne pas cuire les jarres à une température trop basse, sans quoi elles risquent de se briser par réaction chimique au contact d’un sol trop calcaire ou salin.
La production avec ce type de pâte, du fait de sa structure et de la faible épaisseur des pièces réalisées, est sujette à une porosité irrégulière (trop étanche ou micro-fuites) due à l’une ou l’ensemble des phases précédentes.
Toutefois sa production est réalisable en une semaine et donc peu chère à produire, mais se limite à des contenants d’un maximum de 10 Litres.
Si la jarre à pâte « lavée » n’est pas suffisamment perméable, il est possible de poncer légèrement la surface externe, et augmenter ainsi la conductivité hydraulique jusqu’à 30 %.
La poterie ne doit en aucun cas être émaillée.
Cuisson de jarre d’irrigation à pâte « broyée à sec »
A l’inverse, les pâtes « broyées à sec » possèdent un micro-veinage important et régulier grâce à la densité élevée de leur grain naturel et pourront être cuites au-delà de 1.050/1.100°C tout en gardant une excellente porosité, sans excès si on respecte bien le processus de fabrication mais plus complexe et long.
Cela permet de réaliser des jarres de grandes contenances (>35 Litres) qui auront une résistance structurelle élevée et seront insensibles au gel.