Conseguenze della scelta delle argille e dei metodi di lavorazione di Ollas
Per realizzare Ollas irrigui , è necessario scegliere con cura le argille utilizzate e adattare di conseguenza il metodo di lavorazione.
È un processo complesso, su cui Poterie Jamet ha lavorato per molti anni in ricerca e sviluppo per ottenere Ollas che offra il massimo livello di qualità.
Il nostro know-how è al centro di ciascuna delle nostre olla con il controllo di qualità più esigente.
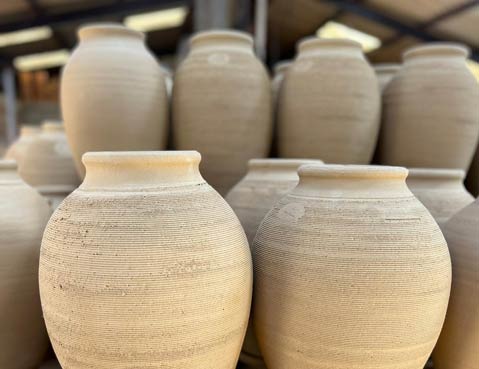
Si tratta per la maggior parte di paste cosiddette “lavate” che vengono immerse in bagni e poi filtrate.
Questo processo ha il vantaggio di avere un materiale poco costoso, veloce da produrre e facile da girare.
Grazie alla filtrazione delle impurità, queste paste "lavate" trattengono poco o nessun granello residuo del terreno, il che rende una pasta compatta con poca aria nelle microvene naturali e conferisce una minore porosità.
Per sopperire a questa mancanza di deflusso dell'acqua, sarà necessario girare vasi con pareti sottili, quindi più fragili agli urti, altrimenti diventerebbero troppo stretti, ma anche più sensibili alle microfessure.
Al contrario, le paste da modellare con terra macinata a secco daranno un impasto a grana naturale permettendo una microvenatura fitta e regolare che conferirà un'ottima porosità e struttura alla ceramica, qualunque sia lo spessore di questa. .
La tecnica del terreno asciutto richiede più strumenti e molto più tempo di preparazione.
A seconda della qualità di produzione desiderata, l'impasto da modellare, dopo il suo impasto (miscela di terra e acqua) e prima della sua estrusione (produzione di blocchi di argilla prima della rivoltatura), può essere lasciato riposare per diversi giorni o settimane a seconda delle condizioni atmosferiche all'ora e sul calendario.
Questa cosiddetta fase di “marciume” – (riposo in linguaggio ceramico), permette ulteriori fermentazioni che garantiscono una perfetta omogeneità di resistenza alla rotazione e all'essiccazione, resistenza dopo la cottura ed infine una porosità regolare.
Questo è un passaggio essenziale che dura almeno 15 giorni per la produzione di ceramiche di qualità.
La progettazione di una pasta per stampaggio con terra macinata asciutta e lunghi tempi di riposo fornisce una materia prima da modellare di altissima qualità, ma è più costosa e richiede più tempo per la produzione.
Inoltre, è meno malleabile delle "paste lavate", che richiedono tempi di tornitura più lunghi durante la lavorazione della ceramica.
Le argille ricavate da terra macinata a secco consentono inoltre di realizzare Olla più resistenti perché più spesse e voluminose grazie alle loro qualità strutturali.
Aiuteranno inoltre ad evitare il conseguente rischio di microfessurazioni durante l'essiccazione, la cottura e dopo la cottura.
Una volta formata la ceramica, è necessario consentire un lungo tempo di asciugatura a temperatura ambiente, che viene regolato in base alle condizioni atmosferiche, alle dimensioni e al peso dei pezzi da essiccare.
Questo permette alle ceramiche di asciugarsi dolcemente, senza fretta, mantenendo intatta l'omogeneità della loro struttura interna.
Questa semplice, ma essenziale, operazione richiede il tempo necessario perché contribuisce alla resistenza meccanica della ceramica e ne impedisce la formazione di crepe e microfessure.
L'essiccazione, effettuata al riparo dal vento e dal sole diretto, permette di evacuare la maggior parte dell'acqua.
La velocità di asciugatura è dovuta principalmente, non alla temperatura, ma a due fattori indipendenti (o quasi):
- Il livello di umidità dell'aria:
Infatti ai tropici con un livello di umidità del 90%, le tue parti si asciugheranno con difficoltà o non si asciugheranno affatto anche con una bassa temperatura di 45°C all'ombra…. - Scambio di gas
Il rinnovo dell'aria asciugherà rapidamente le parti all'aria secca.
Questo fenomeno può portare alla deformazione delle parti, o addirittura alla fessurazione di queste ultime nel caso in cui la parte non si asciughi in modo uniforme e/o troppo rapido.
L'essiccazione rapida è comunque da evitare, soprattutto per la produzione di vasetti per l'irrigazione.
Diversamente, riducendo i tempi di asciugatura, si aumentano ancora di più i rischi di fessurazioni visibili (burst) e non direttamente visibili (microfessure).
Quest'ultimo caso influirà sul funzionamento del vaso che perderà troppo e in definitiva avrà un effetto negativo sulla qualità (*) del terreno. (*) Vedi sezione successiva Microcrack.
Tuttavia, per produzioni di bassa qualità o affrettate, c'è inzuppamento... -> Se sei in ritardo per un ordine e/o c'è troppa umidità ambientale, c'è una soluzione. Il preriscaldamento degli oggetti in un forno evacua l'acqua superficiale prima della cottura vera e propria.
Quest'ultima tecnica consiste nel mettere i pezzi in forno ad una temperatura inferiore a 100°C!
In generale, vengono visualizzati 80°C per... il tempo necessario affinché le parti si asciughino definitivamente. Può durare dalle 3 alle 12 ore o anche più… (qui non siamo in ecologia…).
Il riscaldamento del forno creerà un'espansione dell'aria contenuta nel forno e quindi una leggera sovrappressione al suo interno.
Questo fenomeno evacuerà parte dell'aria riscaldata e creerà un'aspirazione di aria fredda attraverso le aperture del forno (aeratori, fessure, porte, ecc.).
Anche in un forno elettrico avviene uno scambio gassoso tra l'esterno e l'interno del forno.
Questa essiccazione comporterà quindi un inizio del ritiro dal 2 all'8%. Questo fenomeno è dovuto all'evaporazione dell'acqua che si trasforma in gas. Questo fa sì che le molecole si avvicinino.
Le microfessure sono il risultato di un difetto strutturale causato il più delle volte dai seguenti passaggi:
- Elaborazione di pasta da modellare non idonea.
- Tempi di asciugatura e cottura troppo brevi.
- Temperature troppo elevate durante l'asciugatura.
- Gestione della cottura.
Crepe o scoppi più o meno importanti e visibili dopo la cottura rendono la ceramica inutilizzabile. Non può essere venduto così com'è. Nella migliore delle ipotesi, la ceramica verrà finemente macinata per fare una "chamotte" per i ceramisti che necessitano di questo materiale in altre collezioni.
Più difficili da rilevare, le ceramiche che non sono scoppiate all'uscita dal forno, ma che presentano microfessure. Nel caso della produzione di ceramiche per irrigazione, ciò avrà un impatto negativo sulle aree da irrigare.
In effetti, il barattolo micro incrinato colerà molto più del normale. Generalmente c'è un'area di autonomia e irrigazione divisa per 2, o anche di più.
Rilascerà troppa acqua nello stesso posto e in modo permanente.
Questa situazione è peggiore di un terreno troppo secco, perché l'acqua in eccesso ripetuta impatterà/compatterà il terreno, riducendo o interrompendo la vita batterica.
Tuttavia, questo è essenziale affinché la vita microbica e biologica del suolo fornisca suoli freschi e aerati, favorevoli allo sviluppo delle piante.
Per evitare questo difetto, difficile da rilevare, ogni lotto deve essere controllato controllando la porosità dei vasetti.
Fase finale del processo di fabbricazione della giara per irrigazione, la durata, i diversi livelli di temperatura e la temperatura massima di cottura raggiunta, variano notevolmente da uno stabilimento all'altro e dipendono dalle fasi precedenti.
Durante la cottura si creano dei vuoti per evaporazione dell'acqua e degli elementi carboniosi, che rappresentano circa il 20% del volume iniziale (questo non crea un restringimento del 20%).
La modifica dell'argilla mediante cottura consentirà di sviluppare nuove proprietà:
- Resistenza meccanica e termica
- Porosità bassa o alta
- Conduttività termica
- A volte traslucido
A seconda della temperatura massima raggiunta, variano le trasformazioni della pasta e dei prodotti ottenuti (cotto, terracotta, gres, porcellana).
Modifiche della struttura durante l'andamento della temperatura.
- fino a 200°C, l'acqua superficiale viene evacuata (preriscaldamento)
- da 200 a 450°C la materia organica si ossida e viene distrutta a 700°C
- da 450°C a 650°C, la struttura dei materiali argillosi inizia a sgretolarsi
- da 650°C a 800°C avviene la decomposizione del carbonato di calcio
- da 800 a 1100°C si ha una graduale "levigatura" dell'argilla sotto l'effetto dei "fusori"
Partenza dalle diverse acque (da):
- Acqua di imbibizione: > 0°C, durante la formatura
- Acqua colloidale: > 0°C, durante la fase di essiccazione e rassodamento (condizione della pelle)
- Acqua di interposizione: da 23 a 100°C, durante l'asciugatura e all'inizio della cottura (passare allo stato di vapore!!).
- Acqua igrometrica: fino a 350°C, spurgo ad inizio cottura.
- Acqua di costituzione della caolinite: 450°C.
- A 550°C tutta l'acqua è scomparsa, l'argilla non si reidrata più!
Evoluzione delle argille durante la cottura:
- da 0 a 100°C, durante l'essiccazione: partenza dell'acqua di interposizione a 100°C passaggio allo stato di vapore. Rischio di rottura delle parti.
- da 200 a 450°C la materia organica si ossida producendo degassamento. Stesso rischio di cui sopra.
- Point Quartz: quando la temperatura sale, i cristalli di quarzo si dispongono in un ordine diverso.
Intorno a 573°C si verifica una variazione di volume (circa il 2%).
Il quarzo alfa si trasforma in quarzo beta. Questa modifica è reversibile durante il raffreddamento.
Queste variazioni di volume possono provocare la rottura del pezzo se l'aumento o l'abbassamento della temperatura è troppo rapido rispetto alle capacità dell'impasto da formare.
Dovrebbe essere chiaro che queste sono temperature reali al centro dei pezzi e dovrebbero essere prese in considerazione tanto più se i pezzi sono spessi.
Alcune parti possono avere parti di diverso spessore (parti sottili rispetto al resto di esse, pareti sottili su fondo spesso, incollaggio di parti più sottili).
In questi ultimi casi, se la salita è troppo rapida, c'è il rischio di fessurazioni alla giunzione sottile/spessa perché l'espansione non avviene contemporaneamente.
Cottura di un barattolo di irrigazione con pasta “lavata”.
I vasi di terracotta “lavati” vengono cotti a bassa temperatura, inferiore a 1.000°C, per ottenere una porosità effettiva (circa 18-20%, se cotti a 850/1.000°C).
Oltre i 1.000°C, questo ridurrebbe notevolmente la porosità del vasetto, o addirittura lo renderebbe completamente impermeabile.
Questa pasta non presenta sufficienti microvenature, perché troppo compatta per mancanza di grana naturale e unita al restringimento del vasetto dopo l'essiccazione e la cottura, non garantisce la normale porosità alle alte temperature. (>1.000°C°).
Si raccomanda invece di non cuocere i vasetti a temperatura troppo bassa, altrimenti rischiano di rompersi per reazione chimica a contatto con un terreno troppo calcareo o salino.
La produzione con questo tipo di pasta, per la sua struttura ed il basso spessore delle parti prodotte, è soggetta a porosità irregolari (troppo strette o microperdite) dovute ad una o tutte le fasi precedenti.
Tuttavia, la sua produzione è realizzabile in una settimana e quindi poco costosa da produrre, ma è limitata a contenitori da un massimo di 10 litri.
Se il vasetto di pasta “lavato” non è sufficientemente permeabile, è possibile carteggiare leggermente la superficie esterna, aumentando così la conducibilità idraulica fino al 30%.
La ceramica non deve mai essere smaltata.
Cottura di un barattolo di irrigazione con pasta "terreno secco".
Le paste "macinate a secco" presentano invece importanti e regolari microvenature grazie all'elevata densità della loro grana naturale e possono essere cotte oltre 1.050/1.100°C mantenendo un'ottima porosità, senza eccessi se rispettiamo il processo produttivo ma più complesso e lungo.
Questo permette di produrre vasi di grande capacità (>35 Litri) che avranno un'elevata resistenza strutturale e saranno insensibili al gelo.